Much of my mass spectrometry experience has been associated with ICP-MS so I’m far from an expert in thermal ionization mass spectrometry (TIMS), meaning every day can be a school day at Isotopx. Today I was wondering about filament preparation techniques such as carburization to increase efficiency of small samples. However, I thought I’d first look at degassing of filaments, why it’s done, how it’s done, and how Isotopx can help.
Degassing is quite easy to understand – it’s basically used to clean filaments (typically rhenium) before they are loaded in to the mass spectrometer. The degassing process involves evacuating the degassing vessel to high vacuum levels and then resistively heating the filaments. But what’s the benefit? It can significantly reduce the background signal that can come from contaminants such as hydrocarbons and alkali metals. It also helps to volatilize rhenium oxides that could be present as a surface layer on rhenium filaments. So, in layman’s terms it’s a way to burn off contaminants that could otherwise hinder a precise and accurate measurement of the sample.
As always, this is a blog and therefore a personal opinion rather than a company statement. You can address any questions, comments or corrections directly to me (Stephen.guilfoyle@isotopx.com).
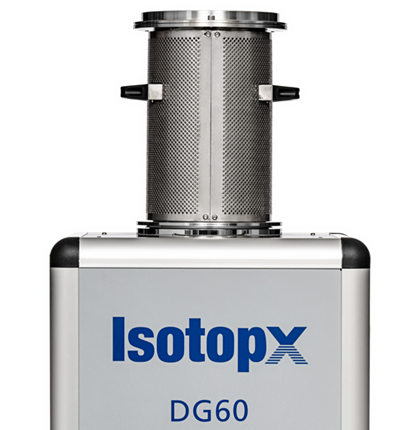
But how long do you degas the filaments for, and at what temperature? That’s where it gets a bit complex. The literature I looked at shows that the degassing duration and current (proxy for temperature when the temperature is not measured) can vary significantly depending on the filament type, sample type and sample size. The degassing temperature is typically above the running current (during sample analysis), but it seems the degassing duration is learned through experience depending on the type and amount of contaminants. In fact, some scientists use more complicated degassing routines, such as ramping the temperature up twice. Take a look at this published article as an example.
Do I have to degas my filaments? No, not every application requires it. However, the smaller the sample, the more significant that potential contamination can be. The literature shows that trace level measurement of uranium, plutonium and other actinides seems to benefit particularly from a degassing stage.
That’s a really simple and non-scientific overview of degassing, now on to the hardware itself. I’ll be shamelessly referring to the Isotopx DG60, firstly as it is the company I work for, and secondly as it is the easiest for me to learn about. If you haven’t seen a DG60, it’s a compact, floor-standing degasser, it looks rather neat. Let’s take a closer look…
How many filaments does it hold?
The DG60 has a capacity of 60 filaments and is capable of degassing in groups of ten filaments, i.e. 10, 20, 30, 40, 50 or 60 filaments per run. Rather than degassing them all at the same time, the degassing is performed sequentially in batches of 10 or 20 filaments. Why do we do it this way? It’s simply to ensure that the DG60 can be operated from a standard mains outlet – a crucial benefit in many labs. Degassing all the filaments at one time would draw a huge amount of power, tripping fuses.
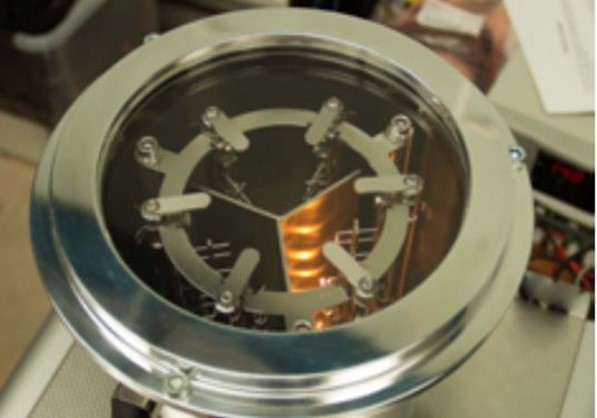
How much control do I have over my degassing method?
What if I want to specify the degassing temperature and time, and what if I want a gentle temperature ramp? This is where the DG60 really comes into its own – it has a huge degree of method configurability. For example, I could set up a method that has a controlled ramp to 4A over a period of 25 minutes, followed by a 5-minute hold at this current. The time per 10 or 20 filament batch would be 30 minutes. If you did this sequentially with three batches of 20 filaments then you’d be looking at a total degassing time of about 90 minutes (plus the time to pump down the DG60’s vacuum chamber).
What about the other filaments that I’ve loaded?
The filaments that are not currently being degassed can optionally be heated to a low level to eliminate absorption of degassed material from hot filaments. Essentially, this keeps them “ticking over” and ready for their degassing stage.
Isn’t it tricky to load the filaments into the degasser?
Actually, no! It’s a “tool free” job, ideal for those with clumsy fingers like mine. Filaments are slotted into DG60 loading racks using a simple push-fit mechanism with filaments being firmly held in place by hidden spring contacts. The spring clips only need to be adjusted during degasser maintenance.
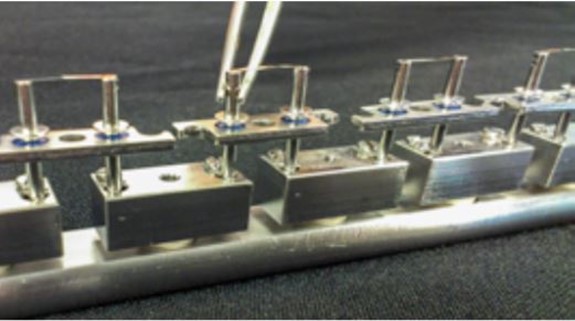
How automated is it once set up?
That’s a real strength of the DG60. It has the has the most advanced software control of any commercially available degas bench permitting a large degree of automation. You can set up different methods for each bank of filaments, then just leave the DG60 to run on its own. It’s even possible to set different temperature ramp steps for each bank of filaments. The DG60 user Interface provides feedback on system status and easy access to pump and vent controls.
What about software control?
The control screen provides visualisations of filament current and vacuum over the course of the run. If you need to intervene, manual control is available at any point allowing you to change the filament current in any one of the six banks within the DG60’s safety limits. There’s also a setup wizard to help you configure your degassing method, always useful the first few times you use a new piece of technology. Another benefit is the ability to see a trace of both vacuum and pressure during the analysis. This gives you the confidence that the degassing went as planned, and identified any issues that might have occurred during the degassing process.
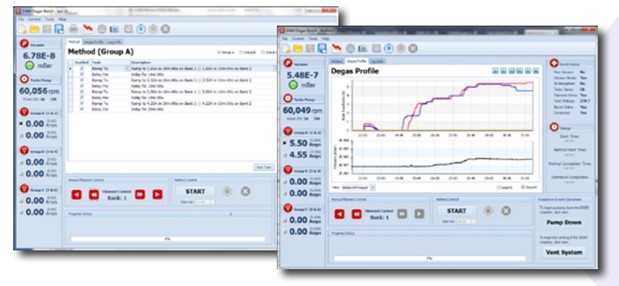
What filaments can I use?
It’s suitable for Isotopx Phoenix, Isoprobe-T (Micromass / GV Instruments) and even VG Sector 54 filaments. What about filaments designed for TIMS instruments from other vendors? We get asked this rather a lot! And the good news is that we absolutely can do this, please get in touch with the team to learn more.
How do we summarise the DG60?
It’s a floor-standing, self-contained filament-degassing unit capable of automatically preparing up to 60 TIMS filaments per cycle. With an ultimate vacuum of 10-8 mbar and easy-to-use software, the degassing of filaments becomes a controlled, reproducible, and hands-off process.
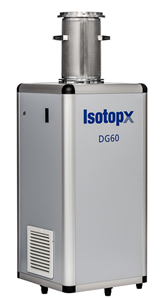
In a future blog post I’ll address carburization. If you have a comment about this post, or wish to point out an error or addendum, please let me know (Stephen.guilfoyle@isotopx.com).