In the world of analytical instrumentation, it’s quite a well-trodden path to move from test and installation engineering to marketing, sales or product management. It’s the route that I took myself, along with a number of my colleagues here at Isotopx. But why does this happen so commonly, what is it about test and installation engineering that works so well as a precursor to product management? And what exactly does a test and installation engineer do? Should you consider it as a career path? Let’s take a look, and as with previous blogs this will be informed by my own background and anecdotal experiences.
I always planned to pursue an academic career, with post doctorate following PhD, following first degree. But during my post-doctorate I got a taste for the faster-flowing and less predictable life that is the commercial world, so I decided it was for me. My scientific career had been in fairly hands-on analytical physics, so naturally I looked to the analytical instrument companies in my job search. The two companies that looked most appealing were VG and Micromass; they both seemed dynamic, progressive, and produced cutting-edge technology.
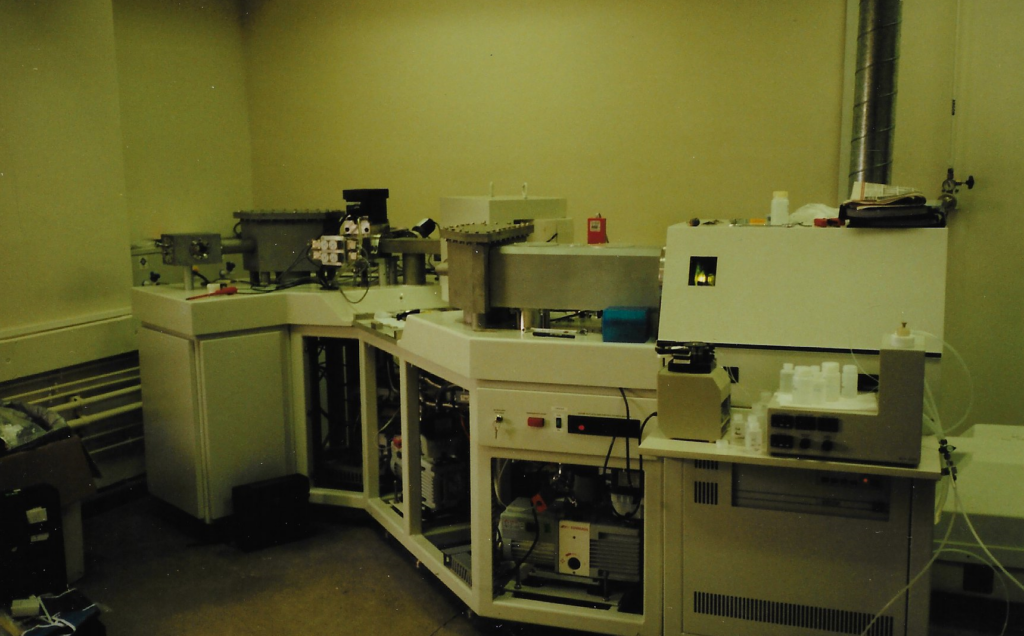
I was already vaguely aware what mass spectrometry was, and firmly associated it with the life sciences. That seemed to tally with Micromass, and when I went for an interview the products I’d be working with were LC-MS instruments of various kinds. But VG Elemental was a little different, their products used something that I found far more exciting, a relatively new technique called ICP-MS. My PhD had involved some plasma physics, so I found this technique extremely appealing.
The role I interviewed for was “test and installation engineer”, which as you might expect, involved taking these cool and interesting instruments through a lengthy test procedure at the factory (possibly taking many weeks) and then travelling out to the site where the instrument would be used, installing it for the customer and training the customer in its operation. This sounded pretty daunting to someone with no mass spectrometry experience at all, but actually I needn’t have worried.
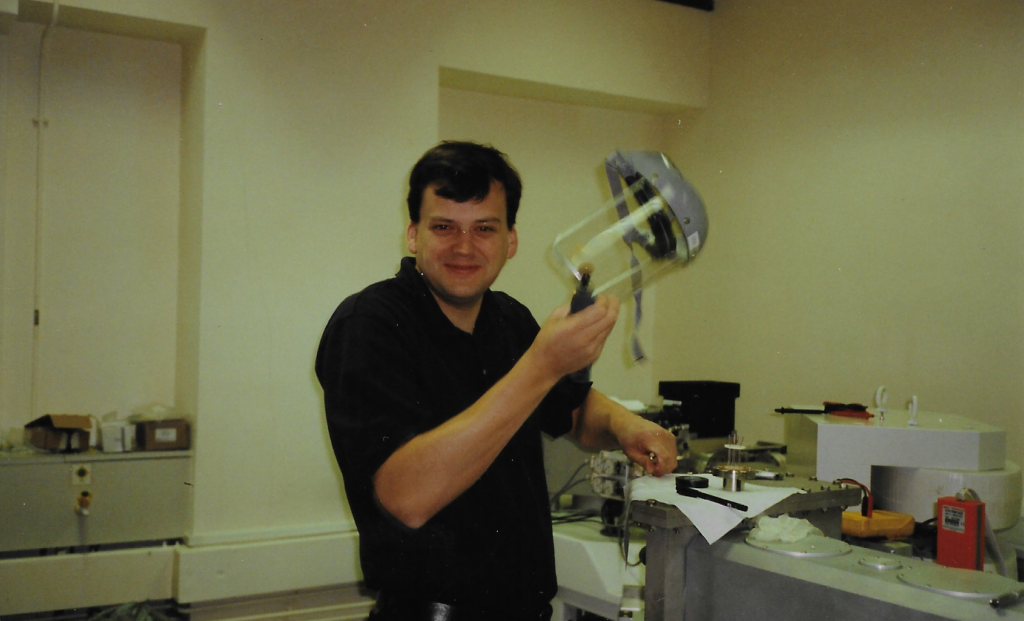
Typically in this role you’ll spend quite a large amount of time, probably many months, working in the factory becoming proficient in the assembly and operation of the instrument before you ever go on site. In my case I spend the first month or two in basic assembly, putting together torch boxes and electronics units. This grounding was essential, I’d never held a soldering iron before this job, so my electronics skills were rudimentary at best.
Before long I was testing the instruments themselves. This process could be time-consuming, any number of electronic or mechanical faults could hinder the operation of the instrument. But nothing felt more satisfying that the first appearance of the eye-searingly bright plasma, perhaps only equalled by the feeling of satisfaction when the computer screen showed an ion beam registering on the detector.
Some analytical instrument companies, then and now, use the same engineer to test and install a particular unit. There are good reasons for this. The first is that during the test procedure you get to know the “quirks” of that instrument – and believe me they do have quirks! The second is that having taken the responsibility of testing the instrument, when you install it if something isn’t right you can’t blame your colleagues. In my experience, the installation would normally take place quite soon after you’d switched it off for shipment, usually just a week or two later.

This brings us to one of the glamourous parts of being a test and installation engineer – the travel to often far flung and exotic places to do the installation. Mass spectrometers are used across the globe and for me, finding out that I’d be installing the instrument in a place I had to look up on a map really added to the excitement. When I started installing instruments, the internet was a mysterious other world that I didn’t have regular access to, and this made the travel even more of an adventure.
Of course, the installation of a half-million pound dollar instrument can take an unpredictable amount of time, making travel arrangements tricky. Typically, I’d book into a hotel for a week or so and then wing it from there. If the first week went well, I’d either extend my stay at the hotel, or if it was full, dig out the trusty White Pages (or it’s equivalent outside the US) and find a hotel the old-fashioned way, by calling each hotel in the area until I found one that was free. The internet generation don’t know how easy they have it!
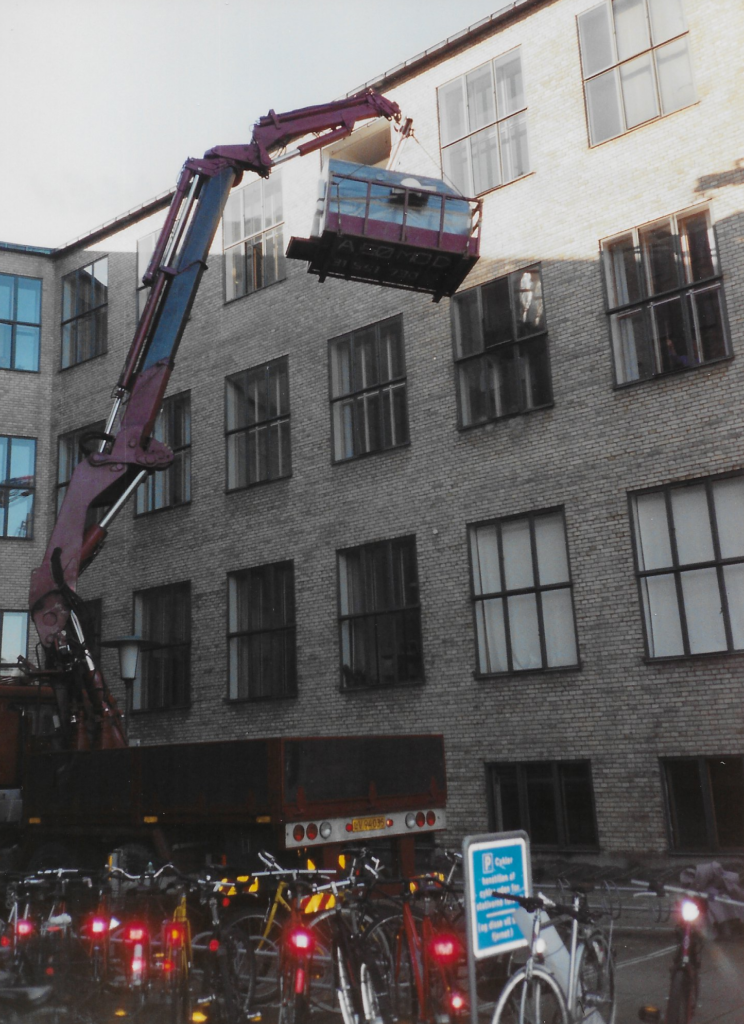
What’s it like at the lab during the installation? Actually, quite different from what I first expected! You have to factor in that the acquisition of the instrument you are installing has been the subject of a huge amount of work by the lab manager or principle investigator (or whomever else leads the project). Sometimes they’ll want a daily (or hourly!) report on your progress, sometimes they will mostly leave you alone to get on with it. But in my experience the scientists I’ve installed instruments for have always been friendly, very willing to help, and extremely grateful when the installation proceeds quickly. In many cases I’ve been able to socialize with people at the lab, making friends and getting the opportunity to really learn about the area.
What about time pressures? It’s true that many labs will be very eager to get the instrument fully operational; keep in mind this is the culmination of years of work for them. But my experience has been that lab managers won’t push you too hard – they want the instrument to work well for many years so if you’re taking unplanned extra time to get something right then they’ll understand. They’ll also facilitate progress by helping out with a replacement if your trusty 3/8” spanner breaks (or if you blow up a 110V monitor using a 240V supply!). In my experience the lab manager will be a font of knowledge regarding spare parts.
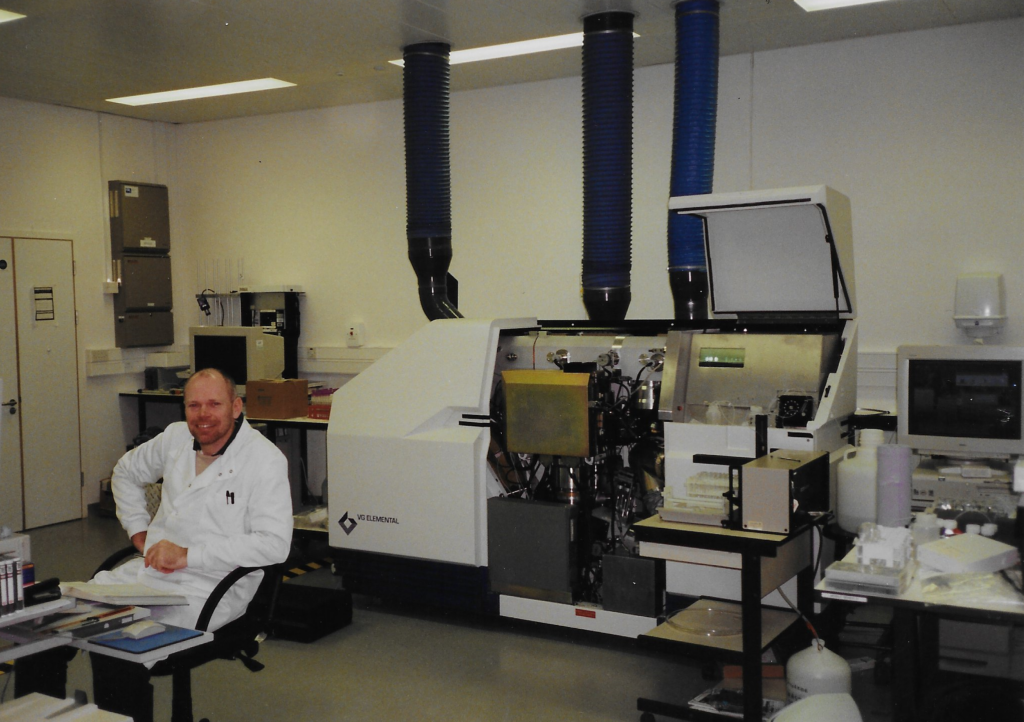
Back to your installation… if the instruments are complex and time-consuming to install, then you’ll also get some weekend time on site. Many labs don’t work at the weekend meaning you get this time to yourself, to explore the surrounding area and often get the opportunity to visit a place you wouldn’t otherwise see. My first three installations outside of the United Kingdom were in Washington DC, New York and Copenhagen. As a young engineer it was impossibly glamorous to be able to stay in these places whilst getting paid for it!
But is it still the same now as when I was a young engineer? Speaking to engineers here at Isotopx it would seem that things haven’t changed much. Some things are easier (hotel booking as mentioned above), and these days the engineers often wear cargo shorts and polo shirts, versus my shirt, chinos, and tie (yes, really). Today’s young engineers still speak about the installation aspect as being interesting and occasionally glamorous.
Would I recommend this as a career path? Most definitely yes; for me it opened my eyes to other cultures, allowed me to develop my resilience and self-sufficiency skills, and ultimately started me on my path to product management and marketing. I’d do the same again.
If you have a comment about this post, or wish to point out an error or addendum, please let me know (Stephen.guilfoyle@isotopx.com).